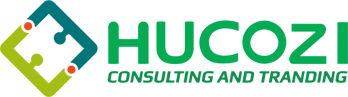
The P&ID. The Pipings and Instrumentation Diagram. An essential element for the successful execution of any capital project and the go-to tool for trouble-shooting and optimizing mill processes. All engineering and operations personnel understand the value of P&IDs, so it is a certainty that the P&IDs for every Pulp and Paper Mill are up-to-date and accurately represent the current processes, right?
Well, not quite. But why not? Is it really all that important? Is it REALLY worth the effort to update and maintain the P&IDs on a continual basis?
In a word, yes. The benefits to future capital projects and every day mill operations mean a better bottom line. Let’s examine.
Why is this the case? Because, like everything, it requires time and money to keep drawings up to date. Also, it is not always easy to quantify the costs of not keeping them up-to-date.
Every capital project should begin with collecting the relevant P&IDs for the mill and verifying their accuracy. If you are going to verify P&IDs as part of a capital project anyway, why not just wait until you have a capital project?
Because verifying accurate P&IDs does not take nearly the time as verifying, marking up, correcting, and re-verifying inaccurate P&IDs. Who has ever worked on a capital project where time was NOT a factor? Schedules are always tight for capital projects. Since you are spending the money to update P&IDs one way or the other, what is that TIME worth on a project? Does it take 200 man hours to update during a capital project? What is that time in actual project schedule? A week? 2 weeks? How much is a week or 2 weeks of production worth? Then, there is the question of efficiency. Is it more efficient to update as changes are made or all at once. If P&IDs were updated as changes were made, would 200 man hours be 100 man hours instead? 50 perhaps?
In addition to the cost impact on capital projects, you also forgo the benefits of having up-to-date P&IDs on operating costs if you only update for capital projects. These costs can be quantified too, though they are indirect and not always seen as a result of not updating P&IDs.
Have you ever encountered these issues in your operations?
Have you ever had to do a study or task force to answer these questions? If yes, what were the states of the P&IDs of the systems in question? Could you turn to your P&IDs and find an explanation? Was there one person on the task force that knew the entire process, or did everyone know “a little bit” of “this” portion or “that” portion? After your study, did you find some aspect of the process that was responsible that was not represented on the P&IDs that caught the team by surprise?
If you answered “yes” to those questions, then THAT is the cost of out-of-date P&IDs. The operating costs forgone and the time and energy spent identifying the problems. Had the P&IDs been updated as the process changed, perhaps that “emergency” tie-in to the fresh water system would not have become permanent. Or, the tie in would have been identified during a simple review of the P&ID by the engineering team.
Keeping the P&IDs up-to-date means keeping the mill personnel’s understanding of the process itself up-to-date! It means not having to have been onsite and seeing the change made, or having to work in that area to know the change was made.
Keeping P&IDs up-to-date means catching problems before they occur, or letting anyone with access to the P&IDs easily troubleshoot problems.
And something worth additional discussion:
Modern CAD programs have abilities beyond just drafting. Even the most basic programs, the programs not designed to tie in to other piping and electrical (Smart) programs, have the ability to store and export data. This is a significant, yet verlooked capability.
Why then, are P&ID’s such a big deal? First and foremost they are the foundational document for the entire process – used for not only design optimization but also Process Hazard Analysis (PHA). What good is a PHA if the drawings on which the analysis is based are inaccurate? How many hazards may exist that cannot be identified and resolved because they are not shown?
Second, they are the foundational document for Process Safety Information (PSI) requirements especially as regards a Process Safety Management (PSM) governed facility. Errors in P&ID’s are usually considered a “willful” violation by OSHA inspectors, and each error can be considered its own violation. This quickly can become a very expensive and damaging finding during an inspection or investigation.
We have found that although P&ID’s may have recently been “walked down”; they often still have many defects or incomplete information. This can be due to a lack of ability or understanding of the team or individual performing the field check, but often the errors occur due to a lack of a systematic approach, or a limiting of scope of the review.
The obvious benefit alluded to previously is the increased safety and efficiency of operations. Perhaps less obvious is the sense of pride and shifting of culture that occurs when all sections of the company observe the attention to detail and importance that management places on safety and accuracy.
We would appreciate the opportunity to visit with you regarding your needs and find an opportunity to show you what the others have learned – HUCOZI is the best back office engineering / design firm in South Africa. CONTACT US NOW.